Structure: brick waste
Anchor is always exploring opportunities to develop new materials from studio waste, which is why we set out to create our own brick waste grog.
Material / 12.2021
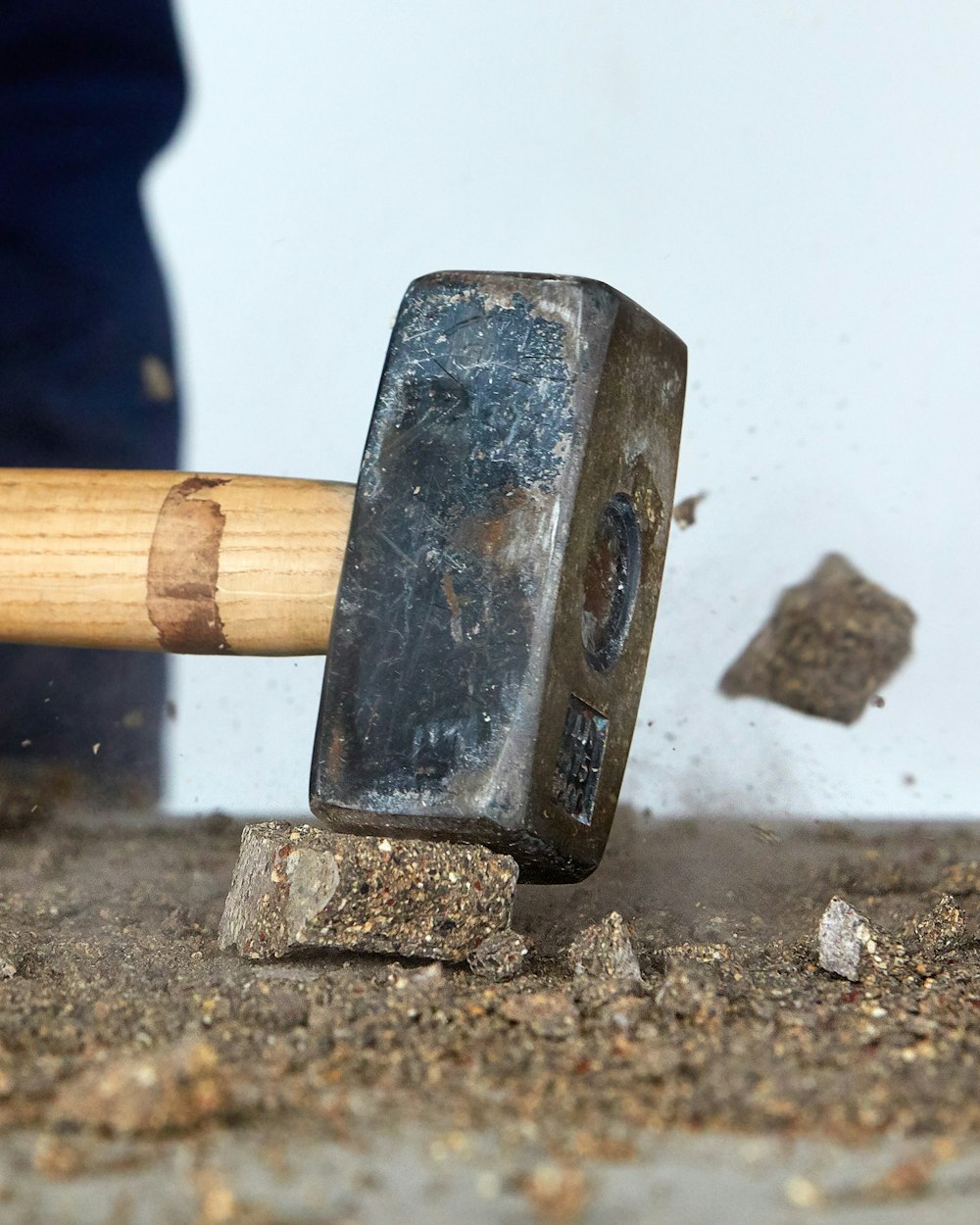
It should come as no surprise to hear that the team at Anchor has a deep appreciation for the humble brick. With a history dating back to 7500 BC, the brick is one of the strongest and longest-lasting building materials. The versatility and prevalence of brick means it’s a constant element of our built environments, and as ceramicists we have a certain appreciation of the transformation of soil to construction element. Plus, there is the added value of bricks as an embodiment of the natural landscape in the urban landscape.
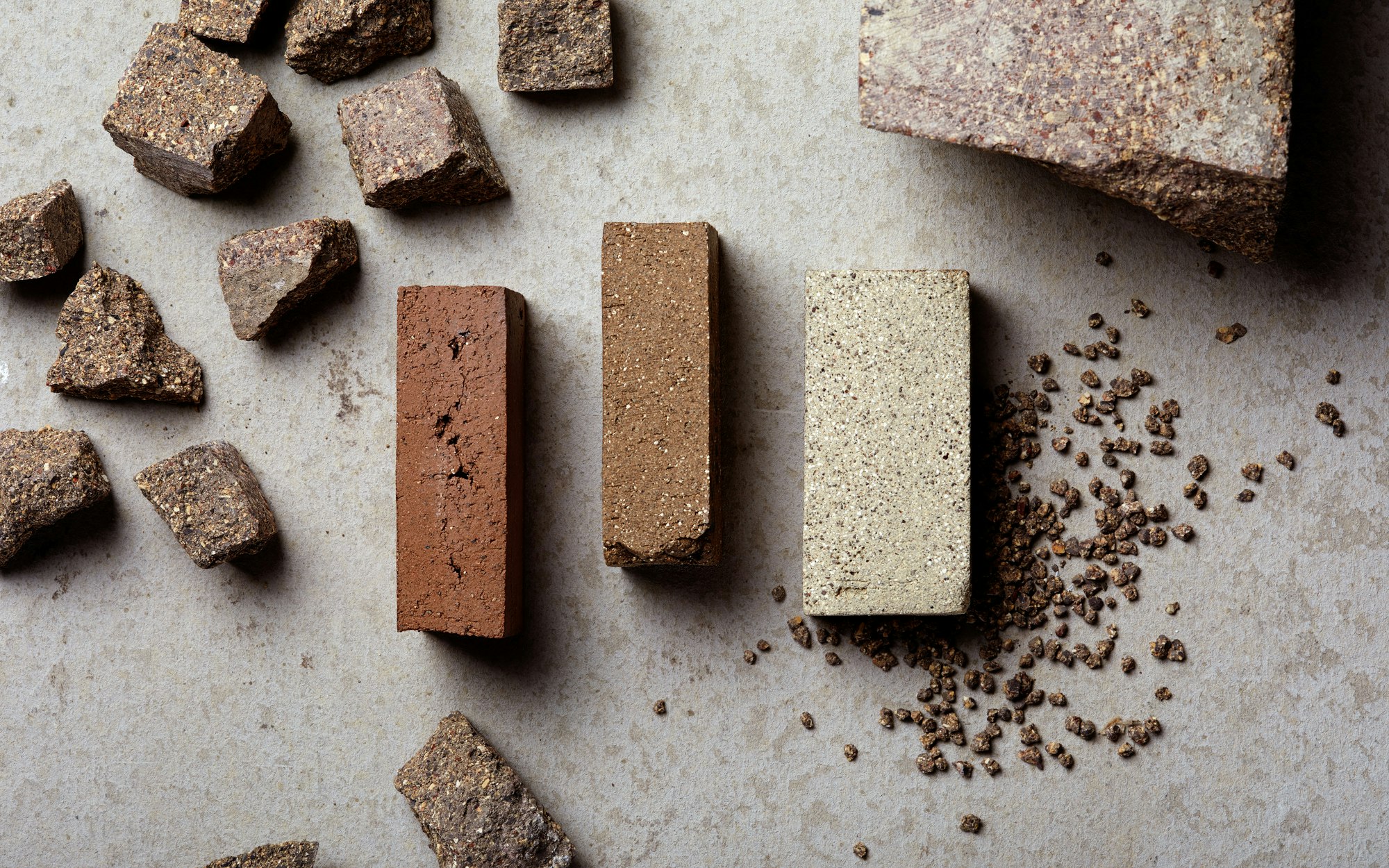
Brick factories often mill their damaged bricks into a ceramic material called grog - it is a process of turning a potential waste material into a sellable building material. The term grog describes a granular material made by breaking down fired ceramic. Grogs are then added to plastic clay bodies to improve drying performance, reduce drying shrinkage, improve abrasion resistance, reduce thermal expansion, and generally to impart visual character.
The percentage of grog used varies widely by clay and application - a sculptural clay typically has 15-25 per cent grog, while a clay designed for press moulding can be made with up to 90 per cent grog.
Anchor is exploring opportunities around waste to develop new materials and so we set out to create our own brick waste grog. Without the appropriate industrial grinding equipment on site, we developed a process of breaking down the brick pieces with a brick set chisel and a hammer. The brick was then crushed, washed to reduce dust and graded into mesh sizes.
The resulting brick waste grog was added to different commercial clay bodies to create a new material palette. When linished to a smooth surface, the test tiles revealed a brindle texture. It also enhanced the performance of the clay by improving its strength, and therefore, reducing the likelihood of cracks during the drying process.
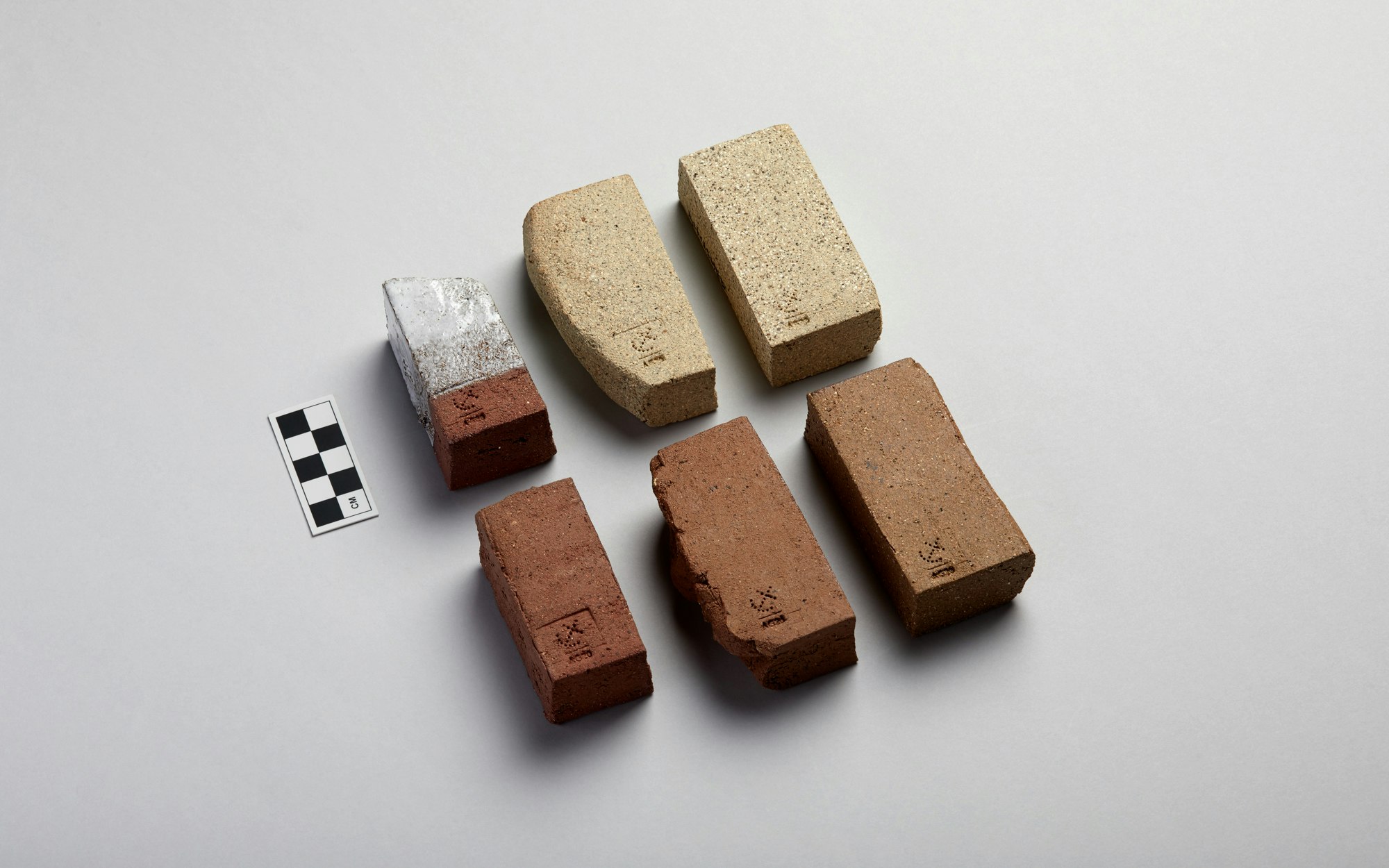