VAS – An Experiment in Research-led Making
The VAS collection is an evidence base as to how radical and unexpected the results of experimental practice-based research can be. We applied design thinking through the process, from material to form to surface finish to create a wholly reimagined vessel made from studio resources diverted from landfill.
Projects / 11.2022
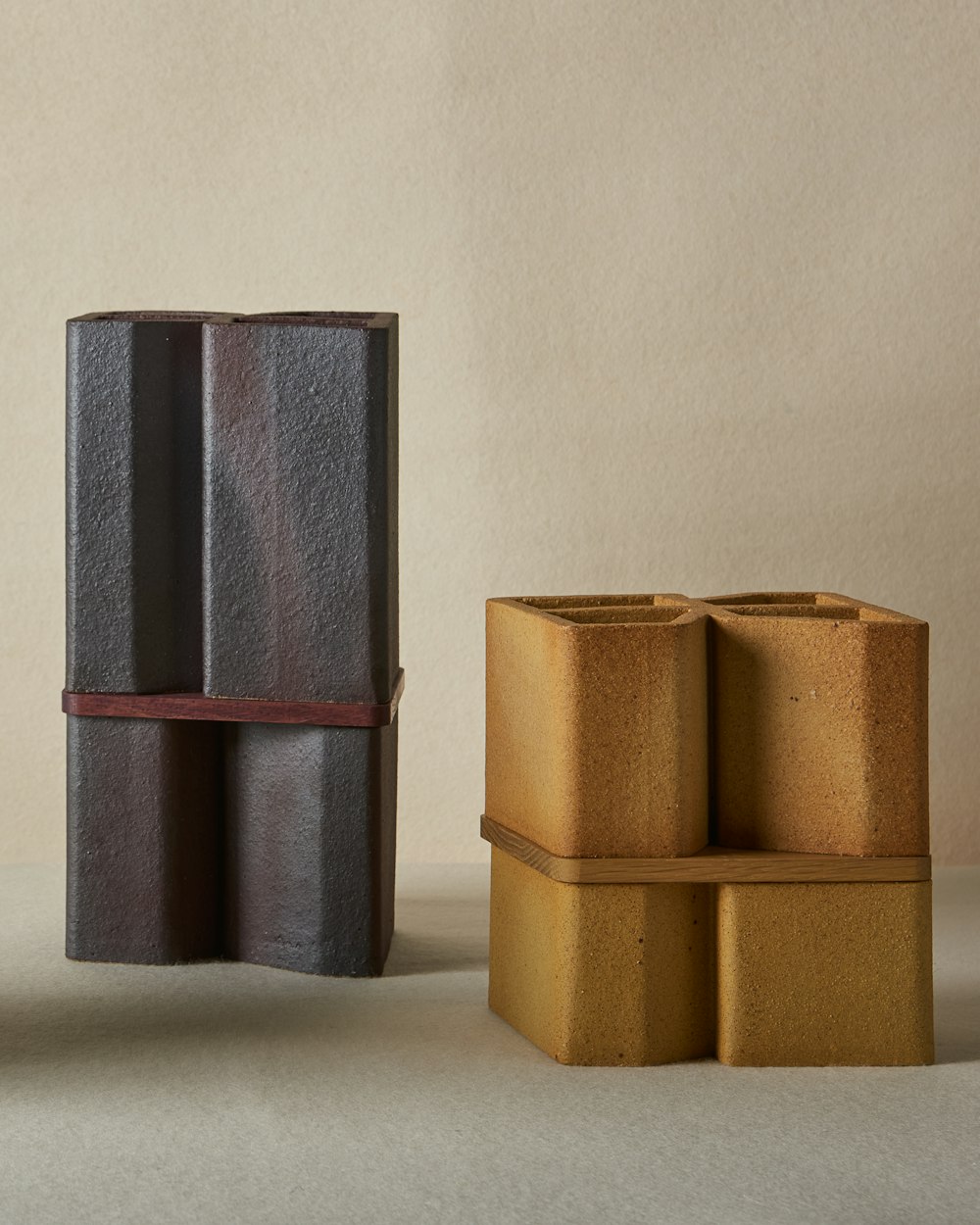
Whether through the R&D program or the team’s background in design thinking and making practices, the creative work is focused on exploring the material possibilities of clay and its potential applications.
VAS is a vessel comprising three interconnecting parts – a base and a top made from fired ceramic, and a middle connecting element made from stained timber. A limited series of 48 vessels have been made, each a unique object by way of size, colour, and surface finish. The VAS project provided a framework for our studio conversations and supported the transition of new knowledge from the arena of research and into its application through the design process.
Anchor’s work on VAS represents these acts of reimagination; from the typology of the vessel as form, to the ways in which studio waste material was repurposed to develop the structural body and the surface of the objects.
Literally, VAS is a vessel that hold many ‘things’ – water, flowers, ideas, care, our practice, design thinking, material research. VAS is a container to both test and hold a multitude of exploratory research streams. During our development of VAS, we held the vessel typology metaphorically and used it as a vehicle through which to mix and combine the seemingly disparate threads of our practice-based research into an object-based outcome. This process allowed the research to shape the result and the design process to inform the research.
If this process sounds linear, or even cyclical, it’s not. Networks or rhizomes are more apt analogies, with each point or node informing the others in a constantly evolving way. It could seem as though the object and its form are the only possible expressions of the research undertaken, the reality is that the object that is VAS now, is just one of an infinite number of possible responses to the material, the research, the vessel typology, and the design process.
VAS is a vessel for four main research streams – repurposing material as structure, repurposing material as surface, the making of large-scale extruded forms, and methods of joining.
The research started with an investigation of the material output of the Anchor studio; clay waste and offcuts that through our production practices become contaminated and unable to be reused through more traditional reclaim methods. The investigation also led the team to think about clay differently. Whilst ubiquitous, clay, even the commercially processed clay bodies used by Anchor, is still the product of finite resources that are formed on geological time.
We hypothesized that through research, we could design a way of making that would allow us to repurpose this material output into a new resource. This new resource became the Studio Process Body; output forming both the matter of VAS’ structure as well as the coloured engobe surface that lends the series their distinctive response to the Australian landscape.
Unlike a surface coating like glaze or paint which is applied to the skin of an object, engobes are instead clay coatings that because they are made from the same materials as the object, have the ability to meld together at a material level and bring forth qualities of the clay to the finished experience of the object. In playing with what qualities of the clay and process could be made visible, we found we could emphasise this tangible sense of the materiality. We found through experimentation we could control the quality of the melt and build up subtle layers of colour, shine, and texture.
In an effort to repurpose as much material output as possible, we chose to utilise the extrusion process. Initial die tests revealed limits to the potential scale of the object before it began to slump. We modified the design, joining two forms into one with interior walls and a faceted form that provided additional strength. Large lengths were then extruded and cut to four heights to create the topology of VAS. The 80mm and 120mm cuts were joined with slabs to create watertight bases, and the 100mm and 180mm lengths were left open to connect through a timber insert to the base. With the added element of the three colourways, these create the open and modular vessel form of VAS. The insert introduced a new material quality to the project and cushioned the often-harsh aural friction of ceramic on ceramic.
Anchor’s R&D Lead, Amelia Black, says “The materia that makes VAS carries with it the patina of studio work, bits of grog from one project, iron rich clays from another – all come together to form something entirely new. Work around the surface came from a desire to highlight these qualities and textures of the Studio Process Body. We added water and fritted fluxing agents to transform the structural material into a brush-able finish that would melt into the form. The qualities of the melt were further highlighted through the application of flux washes.”
Light, shadow, colour, and texture are resolved through the individual surfacing finishing process. Each of the 48 vessels in the series is distinctive in finish, made through an inventive and kinetic flux wash application technique. A flux is a material that when heated melts readily and that can increase the melt of the material on which it’s been applied, thus revealing an inherent chemistry of those materials.
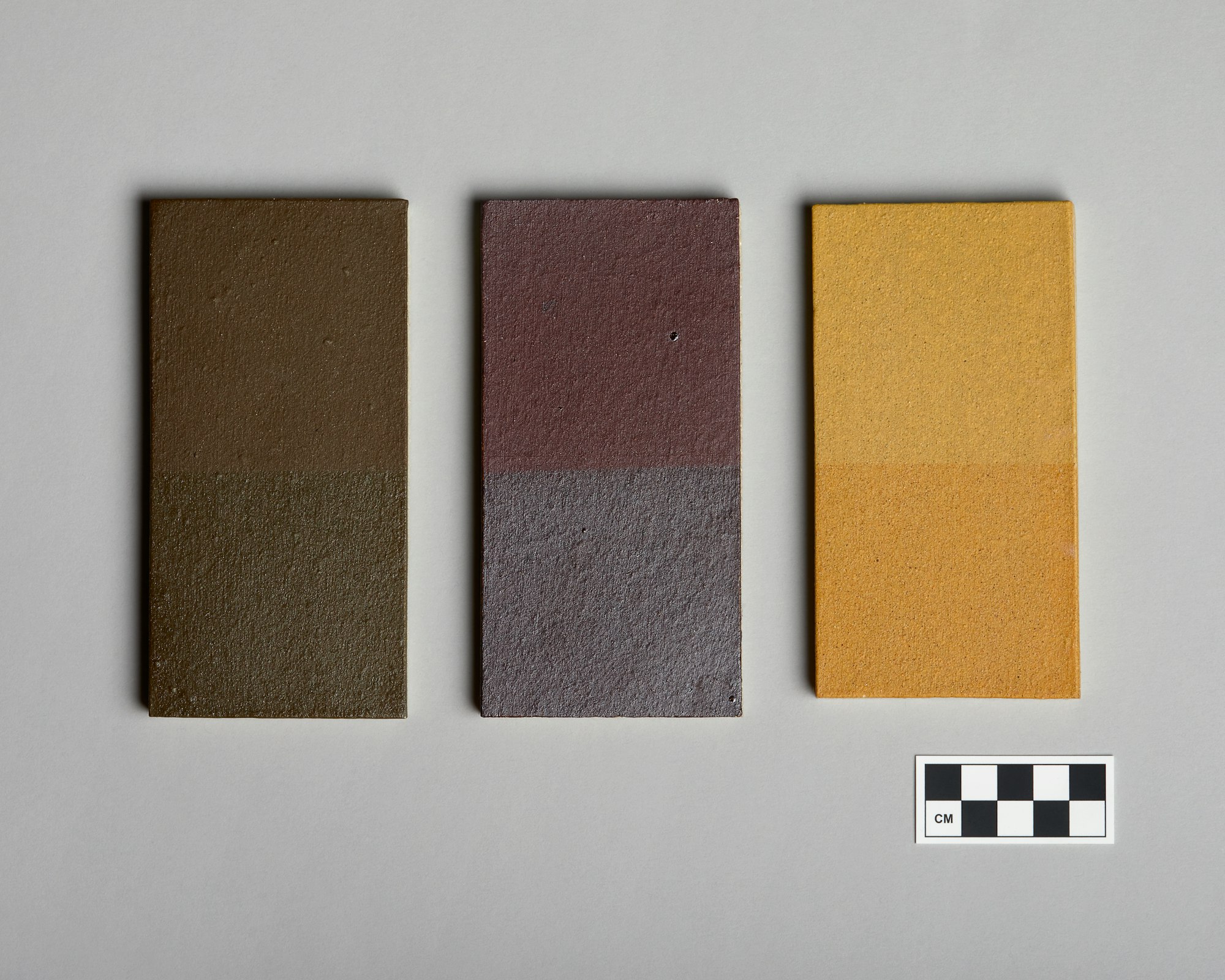
The surface of each VAS was developed through a process of observation and drawing, resulting in a masking technique using voluminous foam objects to create singular patterns in the spray application of the flux wash. The colour palette that emerges over the course of development is strongly evocative of the south-eastern Australian landscape and brings together the team’s exploration of different greens as well as a deep dive into oxidized metals as a source of colour – in this case red and yellow iron oxide, resulting in the rich monochromes we are calling Wattle, Banksia, and Iron Ore.
Anchor’s Creative Director, Bruce Rowe says “The VAS collection is evidence to how radical and unexpected the results of a gradual process of experimental practice-based research can be. We applied design thinking throughout the entire process from materia to form, then surface finishes to create a wholly reimagined vessel made from studio process resources.”
Project Team
Bruce Rowe, Creative Director; Claire Hatch, Director; Angus Gardner, Making Lead; Amelia Black, R&D Lead; Kendall Manz, Studio Assistant
Acknowledgements
VAS timber work: Andrew Lowe - Lowe Furniture // VAS Exhibition construction: Piers Brown - Plan Build // VAS photography: Lisa Cohen // Research artefact photography: Tatjana Plitt